Industry 4.0
Turning Concepts into Reality
INDUSTRY 4.0
This indicates a commitment to innovation and leveraging advanced technologies to enhance operational efficiency and effectiveness.
Connecting Industry 4.0 systems with the Enterprise Resource Planning (ERP) system ensures seamless data flow and better decision-making across the organization.
Providing technicians with easy access to relevant documentation and models can streamline processes and reduce errors.
Automating the transfer of programs from the central system to machines to improve productivity and reduce setup times.
Having real-time insights into production capacity enables better resource allocation and scheduling.
Generating reports with graphical representations simplifies data analysis and decision-making for managers and stakeholders.
Monitoring operator efficiency helps identify training needs and optimize workforce performance.
Tracking quantities manufactured, rejection rates, and rework instances is crucial for maintaining product quality and process efficiency.
Predictive maintenance based on real-time machine health data can reduce downtime and extend equipment lifespan.
Tracking inward and outward movement of components, especially for outsourcing processes like surface treatment, ensures smooth supply chain operations.
Supporting the transition from 2D to 3D modelling reflects adaptability to evolving design and manufacturing trends.
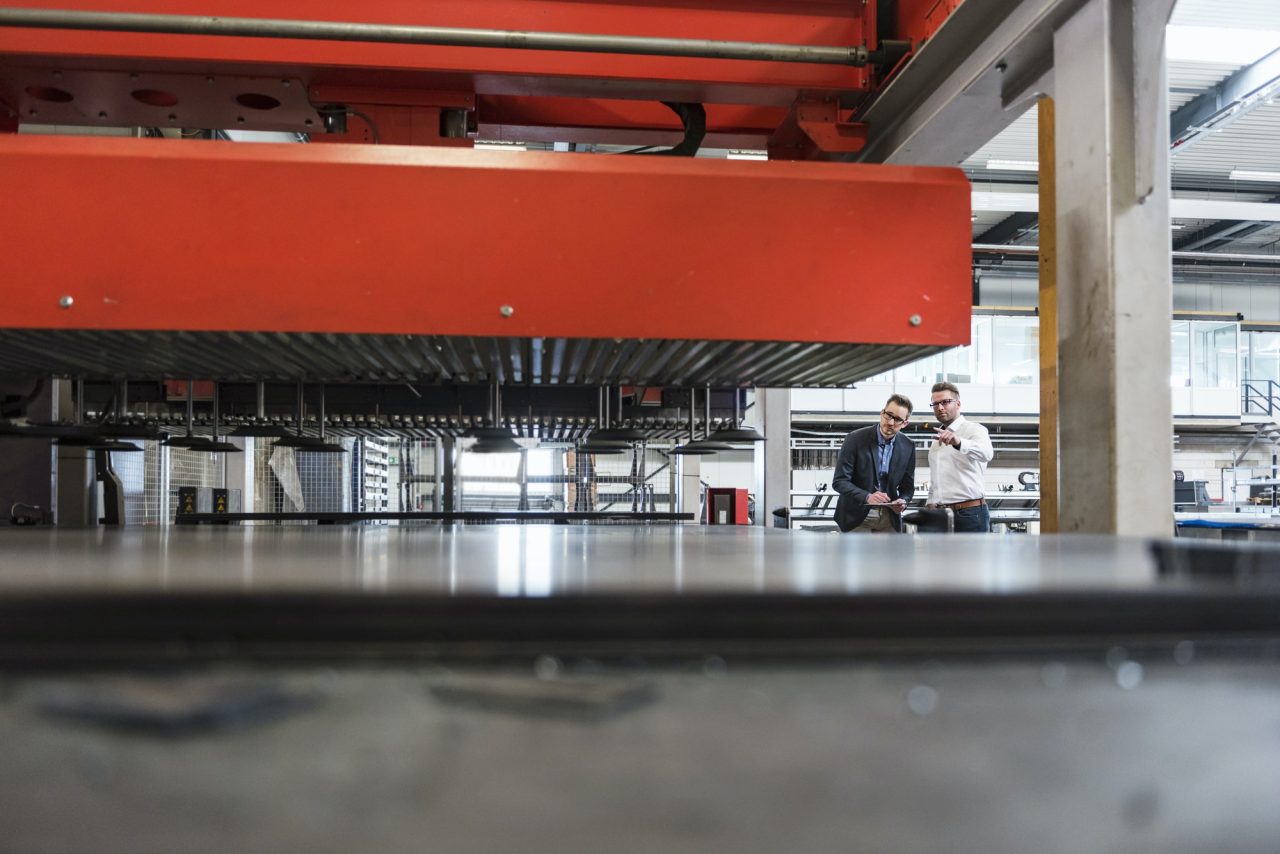
This indicates a commitment to innovation and leveraging advanced technologies to enhance operational efficiency and effectiveness.
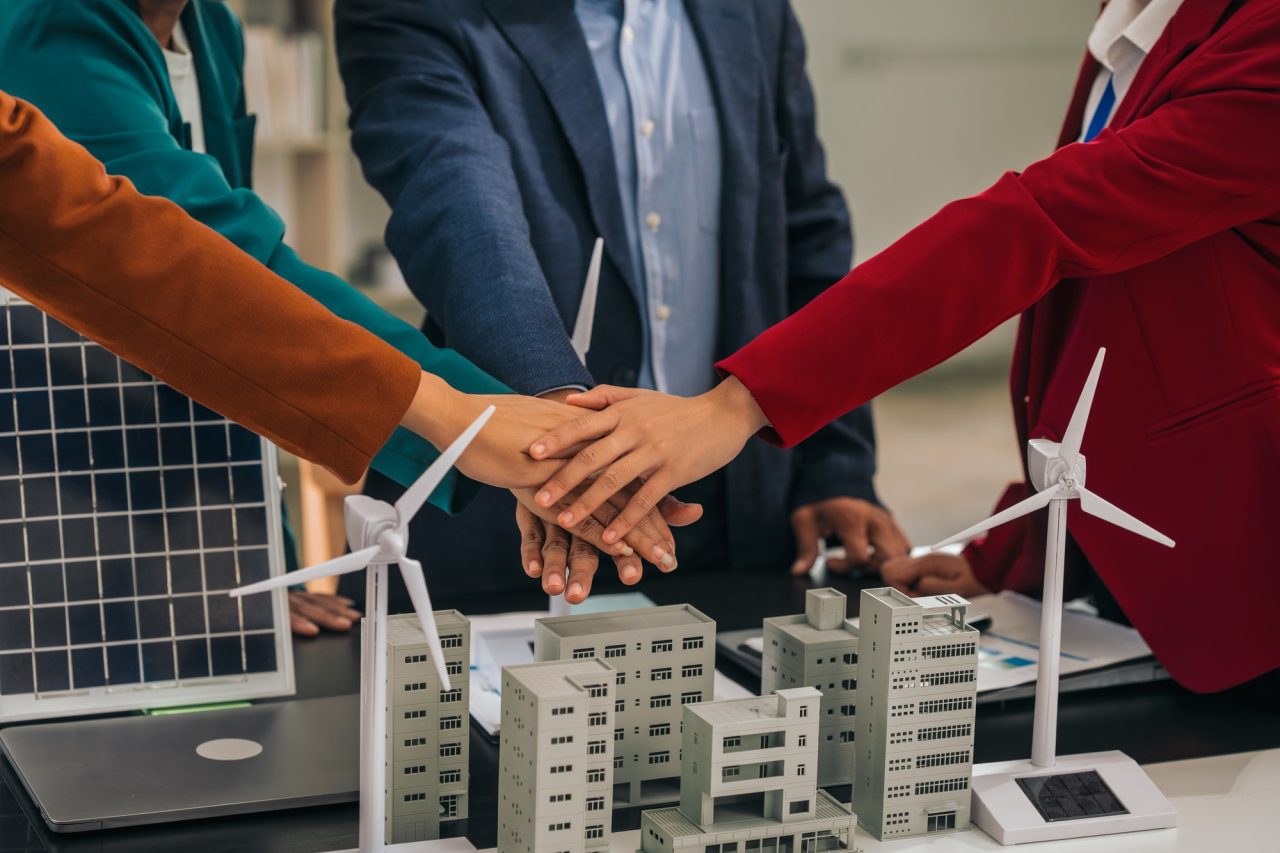
Connecting Industry 4.0 systems with the Enterprise Resource Planning (ERP) system ensures seamless data flow and better decision-making across the organization.

Providing technicians with easy access to relevant documentation and models can streamline processes and reduce errors.

Automating the transfer of programs from the central system to machines can improve productivity and reduce setup times.
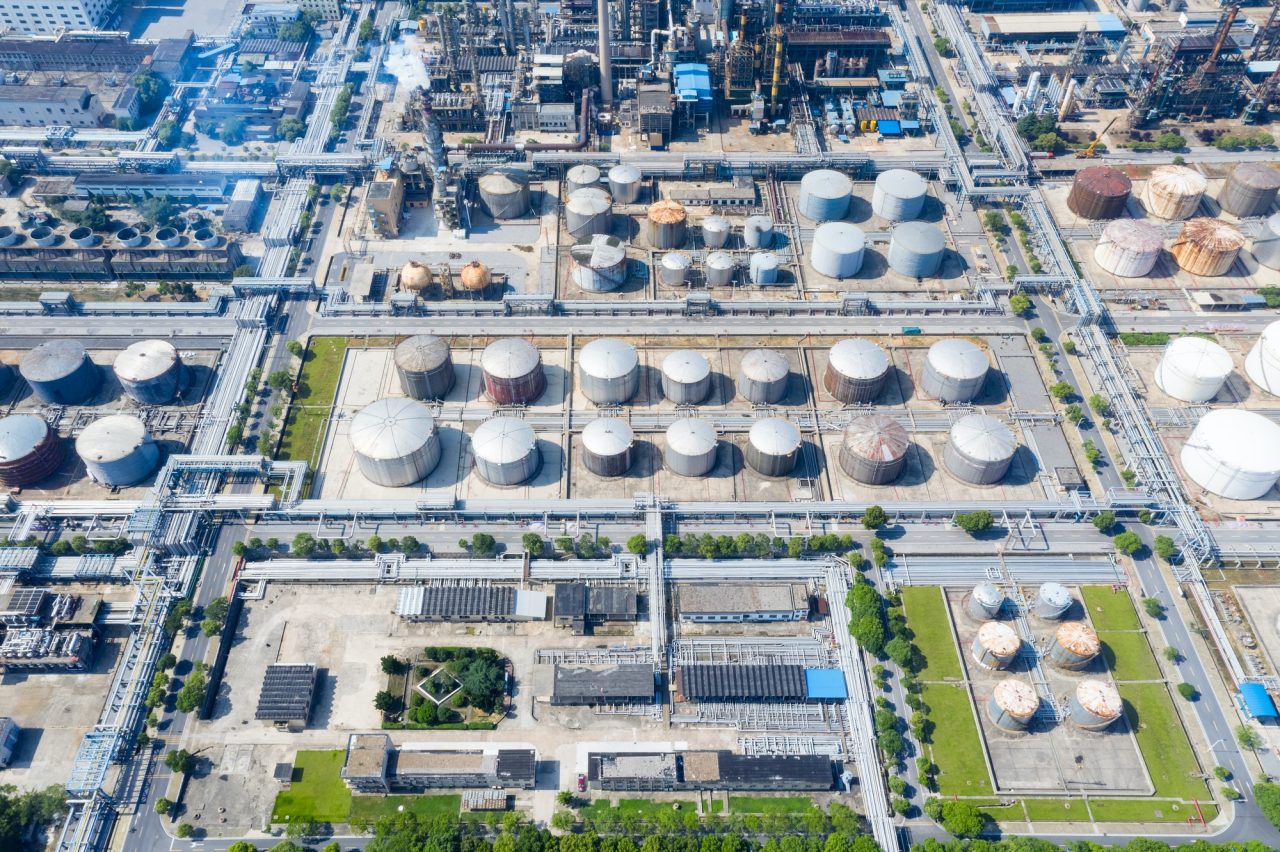
Having real-time insights into production capacity enables better resource allocation and scheduling.
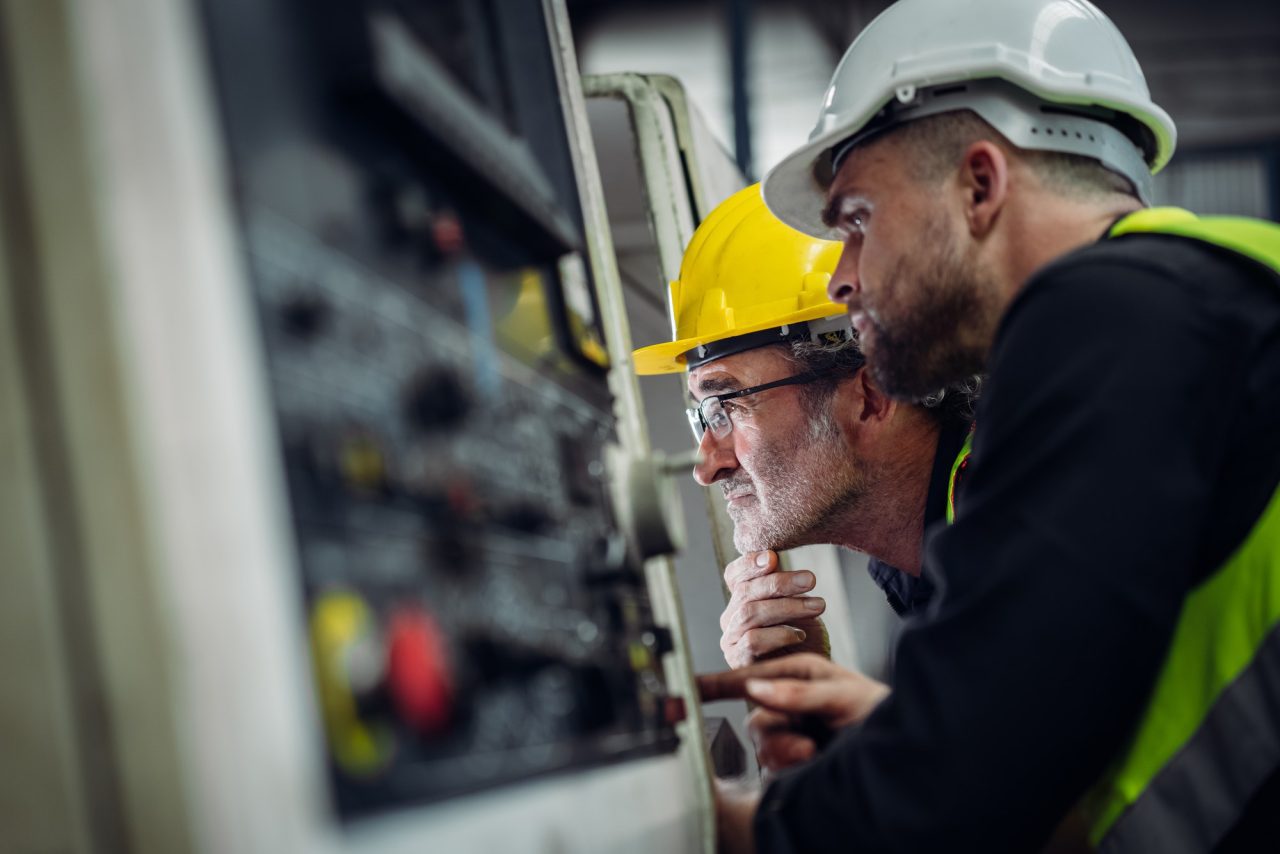
Generating reports with graphical representations simplifies data analysis and decision-making for managers and stakeholders.
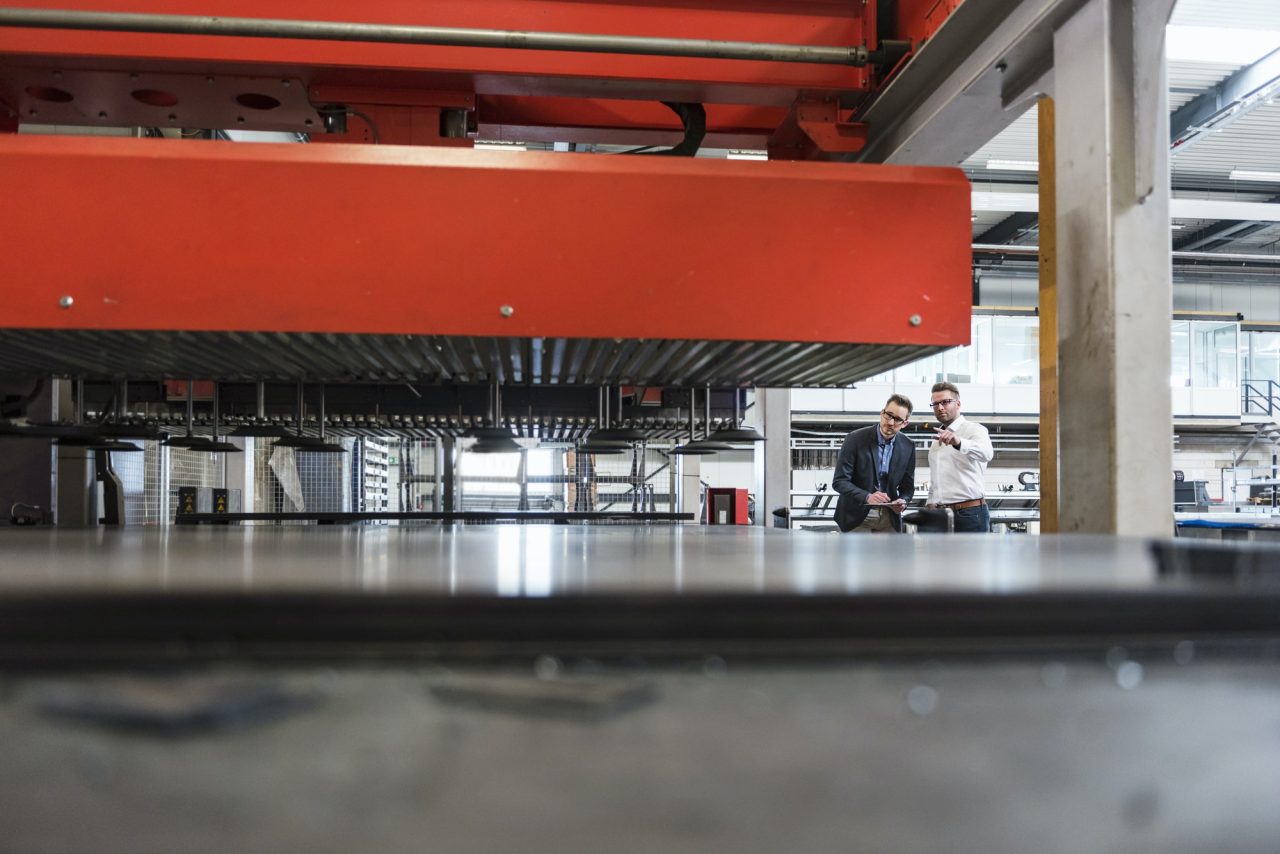
Monitoring operator efficiency helps identify training needs and optimize workforce performance.
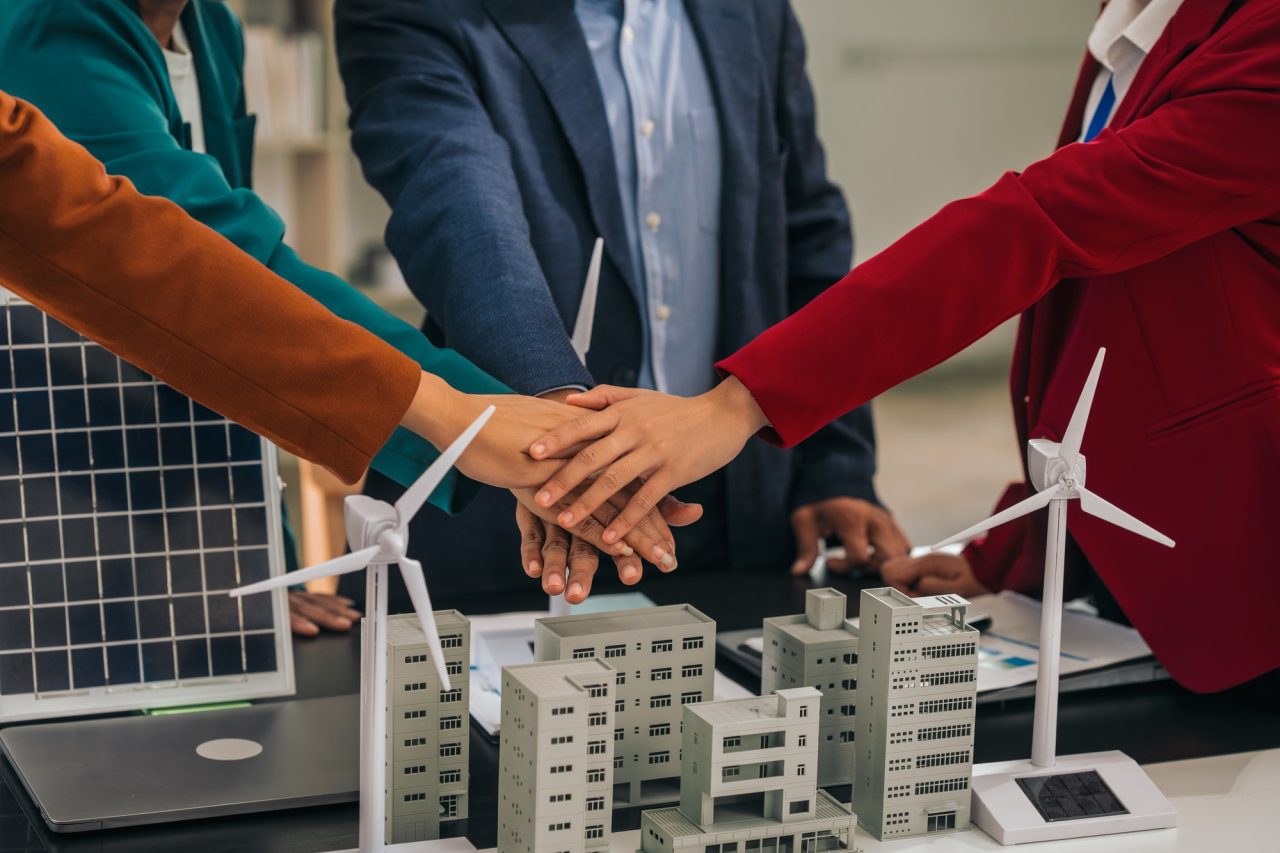
Tracking quantities manufactured, rejection rates, and rework instances is crucial for maintaining product quality and process efficiency.

Predictive maintenance based on real-time machine health data can reduce downtime and extend equipment lifespan.

Tracking inward and outward movement of components, especially for outsourcing processes like surface treatment, ensures smooth supply chain operations.
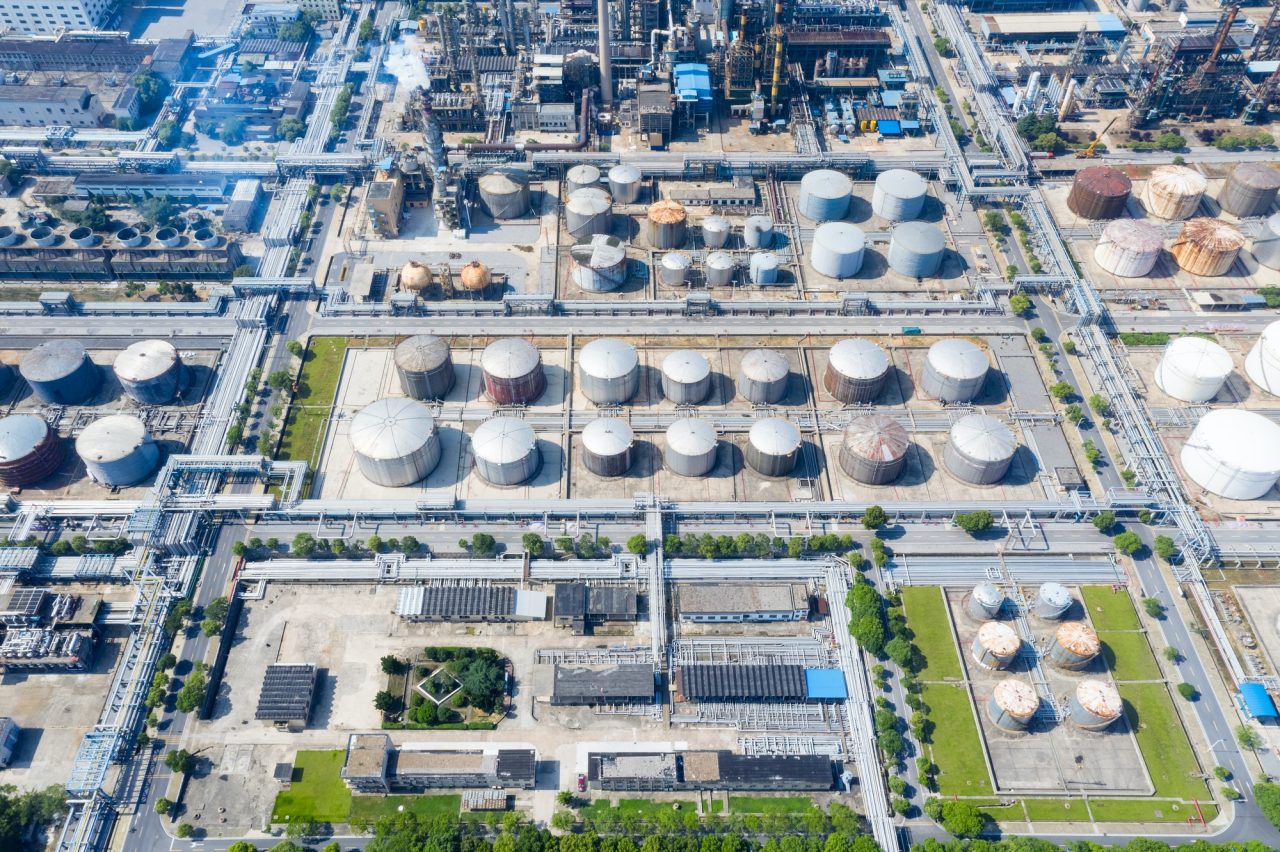
Supporting the transition from 2D to 3D modelling reflects adaptability to evolving design and manufacturing trends.
Let's start your project
Connect with us today for high-quality, customized solutions in all areas of precision engineering.